Packaging is essential for safely storing and transporting food from factories to supermarkets, shops and restaurants and finally to peoples’ homes. Creating and manufacturing fit for purpose packaging and plastic requires sophisticated innovation and engineering, so that food stays fresh, quality is maintained, and food waste is kept to a minimum.
Our strategy focuses on removing unnecessary plastic, increasing recyclability and recycled content in our packaging, while removing complexities and designing products in support of a circular economy. We have a strong partnerships with our packaging suppliers and work in collaboration to make sure any new solutions we roll out will have long-term sustainability benefits.
We are members of REPAK and WRAP’s UK Plastics Pact, working to achieve the 2025 and 2030 targets to eliminate problematic plastics, stimulate innovation and new business models and help build a stronger recycling system.
Achieve the REPAK and UK Plastics Pact Targets by 2025 and 2030
Target One:
100% of our plastic to be re-usable, recyclable, or compostable by 2025
Plastic trays and flexible materials such as films are excellent for protecting food during transport and while in storage, as they have high puncture resistance & gas barrier properties which keep water and air borne bacteria from coming into contact with food. Over time, packaging has increased in complexity to extend product shelf life while maintaining product quality. Using several types of plastic in a single pack makes it harder to recycle, and we are working to simplify the structure of our packaging to enhance its circularity, while maintaining food safety and quality and maximising product shelf-life.
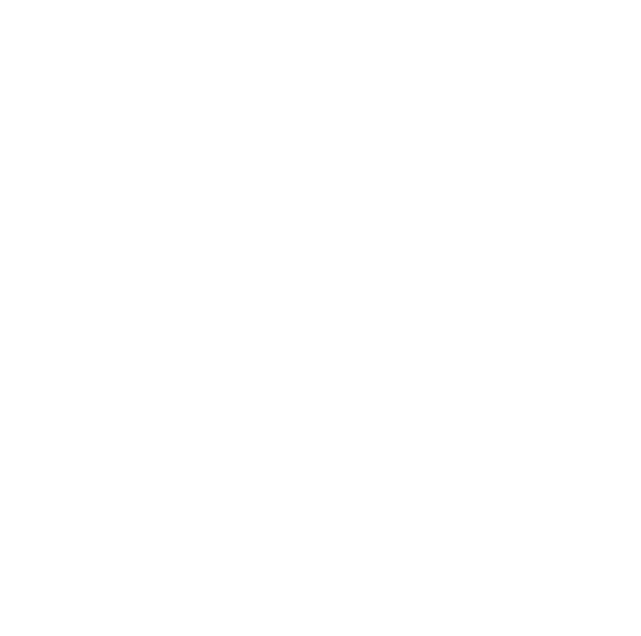
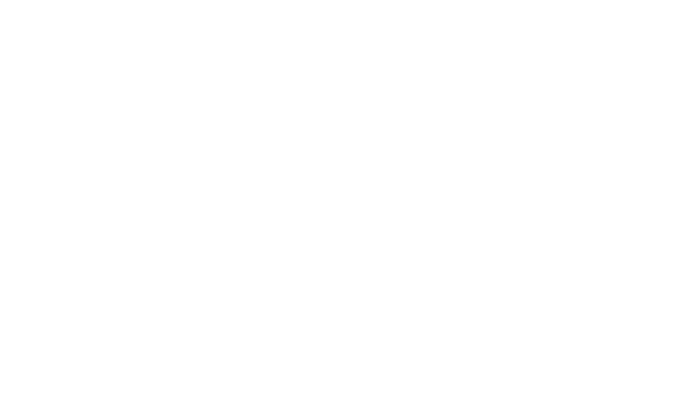
A fully recyclable tray is a key step to achieving a circular economy for plastics and will help to increase PET recycled content. We developed and introduced a first to market solution for retail Vacuum Skin Packaging trays, which are made from a material called Mono rPET, or recycled mono polyethylene terephthalate, which is clear in colour and fully recyclable. In conjunction with our machine and plastic suppliers, Mondini and Sealed Air, we then took this solution a step further to reduce the flexible film used of our mono skin packs by 25%. In 2021 we launched mono skin for Darfresh On Tray PET using new mono sealing technology, which allowed us to continue delivering mono skin pack trays with zero film waste.
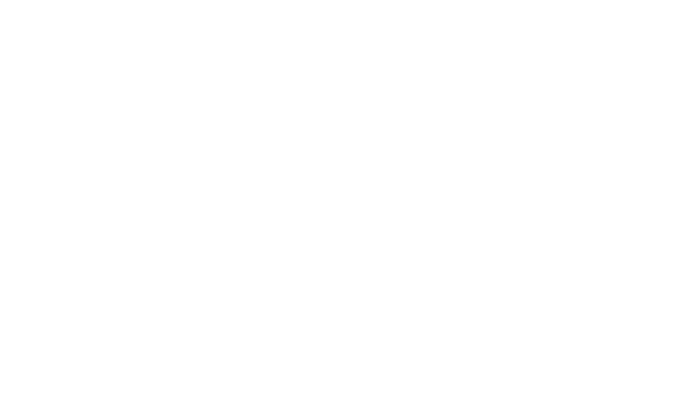
Flexible materials such as shrink bags and films are laminate structures made of multiple plastic types, with valuable characteristics of puncture resistance, barrier properties and excellent sealing ability. We are collaborating to explore solutions for flexible materials which are challenging to engineer using a single plastic type such as shrink bag and films, and we are key stakeholders in smart sustainable packaging projects with Innovate UK and Meat Technology Ireland.
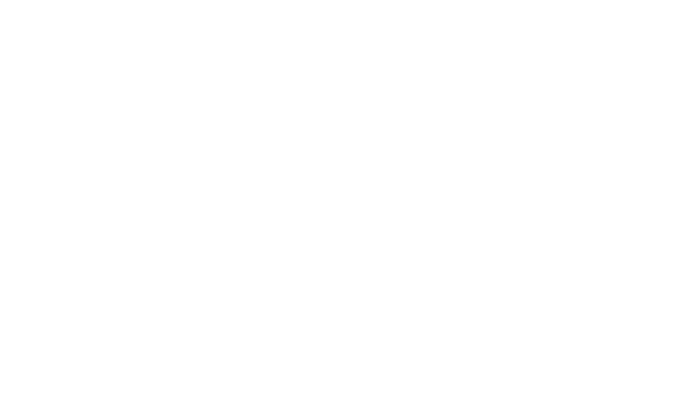
The HiBarFilm2 Project is an Innovate UK funded project that started in March 2022 and is expected to run for 30 months. Haydale Composite Solutions Ltd is leading the consortium of nine companies to develop the next generation of high barrier films for food packaging using functionalised nanomaterials. The project has an ambitious objective to achieve the same barrier performance using a mono-materials polyolefin film as the currently used multilayer barrier films. By manufacturing mono-material flexible films the recyclability of these materials will increase, and value will be added.
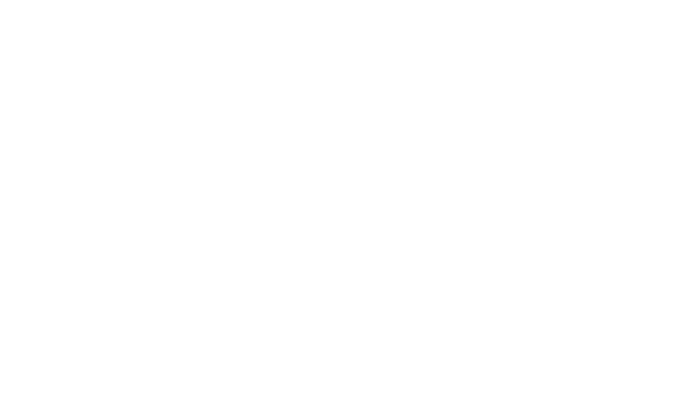
Upcoming EU regulations are targeted at ensuring all plastic packaging is recyclable or compostable by 2030. Hence, the design of sustainable packaging alternatives for circularity is of utmost importance. Both meat primal and retail packaging structures, face their own environmental challenges related to the carbon footprint associated with their production and efficiency in terms of food safety, circular economy and their end-of-life options. This Meat Technology Ireland project aims to assess existing packaging offerings and redesign and optimise identified flexible packaging structures and reduce emissions. It also aims to enhance packaging recyclability and identify biodegradable packaging constructs suitable for meat packaging applications which will allow the expansion of their supply chain and the transition to a circular economy.
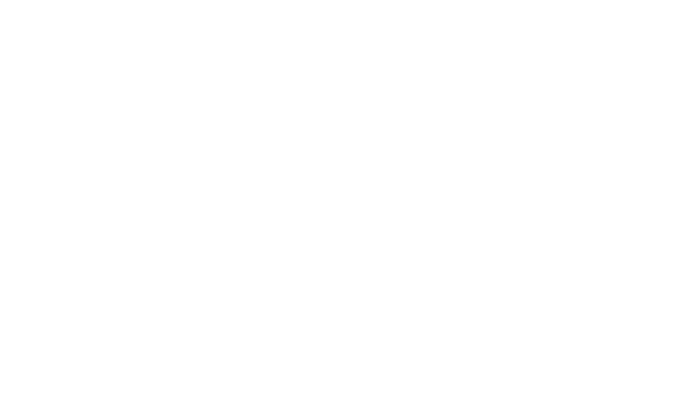
We are members of On Pack Recycling Label, working towards solutions that can deliver on existing and new guidelines being introduced. In 2020, circa 67% of the total plastic used was classified as On-Pack Recycling Label “Recycle”. Solutions are being explored which will increase the proportion of packaging which can be deemed as OPRL Recycle. This will be aligned with the infrastructure and roadmap for Flexible packaging.
Target Two:
30% average recycled content across all plastic packaging by 2025
Making virgin plastic requires the use of hydrocarbon technology, a process which involves the release of GHG emissions. It is really important to use recycled materials whenever possible and key to creating a circular model for plastic packaging will be the development of national policies and collection and recycling infrastructure.
Virgin materials often present themselves as commercially favourable due to the demand for recycled materials, and this poses a significant challenge in an economy where prices are rising. There is uncertainly around the continued availability of good quality recycled content, and markets are monitored closely to ensure we are ready to align with new guidelines and requirements.
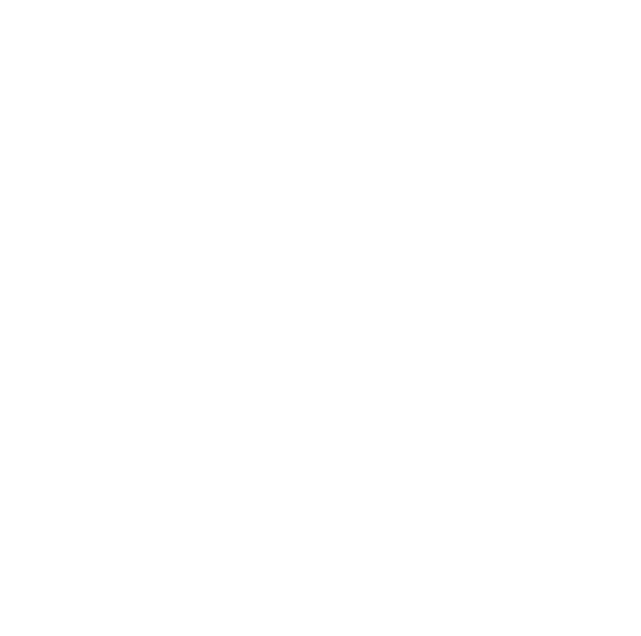
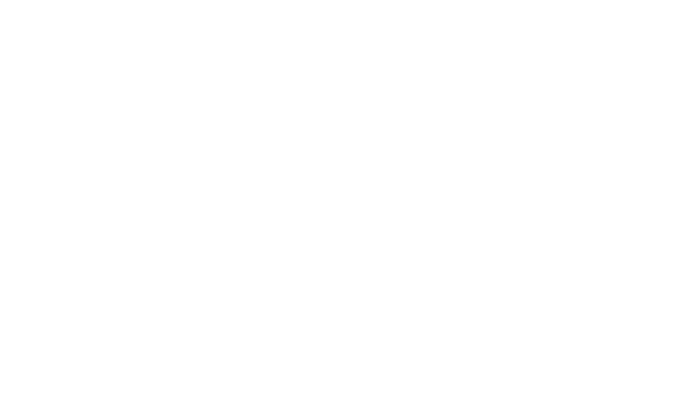
PET from plastic bottles is the primary source of recycled material used in our trays, which can have an average recycled content of up to 90%.
Material availability for recycled content is a challenge. European legislation requires increased recycled content for bottle manufacturers and industrial consumers, with 30% as the stated minimum. We are supportive of measures to promote tray-to-tray recycling streams and a circular economy and are engaging with suppliers to understand the market.
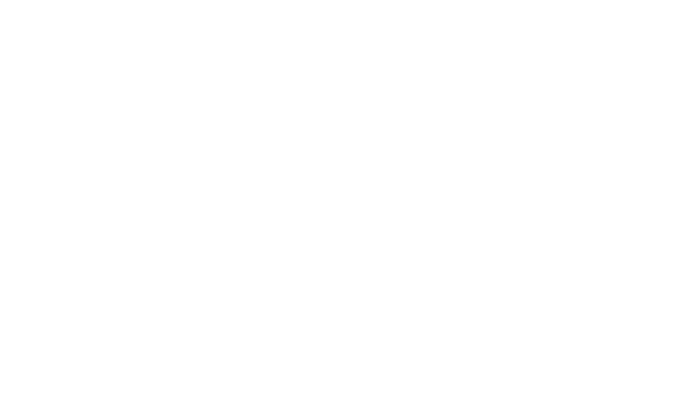
Sourcing recycled content for flexible materials, such as MAP lidding films, VSP skin films, vac pack pouches and shrink bags is a significant industry challenge and we are working with suppliers to understand new and emerging technological solutions. Since 2021 in Ireland all soft flexible packaging can go into domestic recycling for energy recovery, which is a good interim solution to avoid landfill, but we must keep focus on making packaging material circular.
In 2022 we introduced a lidding film for MAP applications with a 30% recycled content, which delivers a 12% reduction in plastic, and this technology is scheduled for deployment across the remaining retail packaging sites by the middle of 2023.
Target Three:
Prioritise the prevention of plastic packaging waste, eliminate problematic or unnecessary single use plastic by 2030
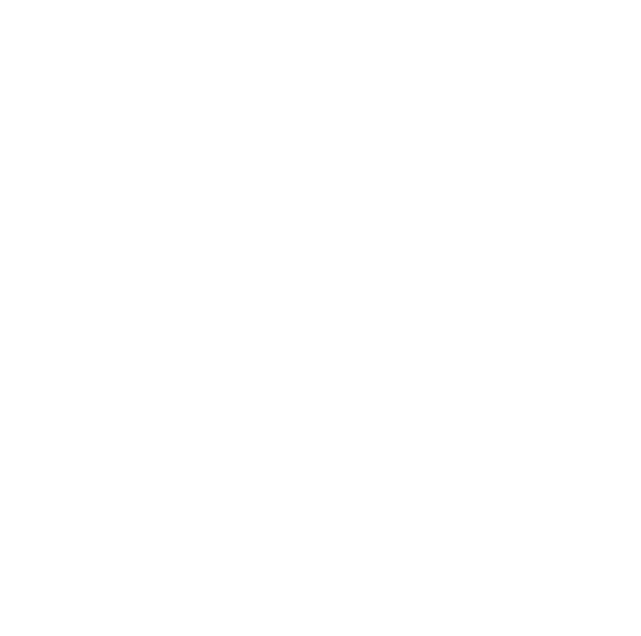
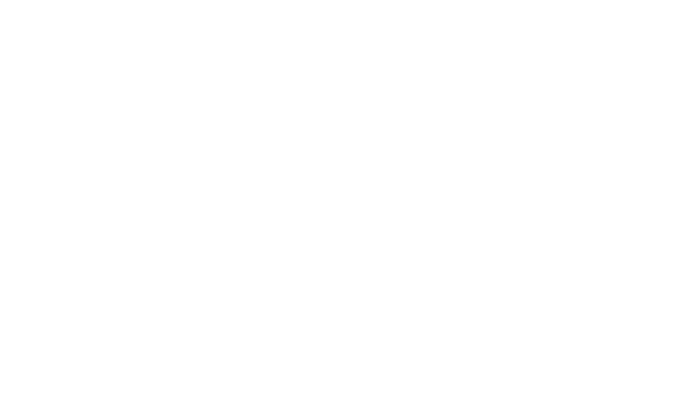
We continuously review relevant packaging supply chains to identify opportunities for plastic reduction through value engineering projects and innovative tray redesigns. Since 2019 we have achieved a 14% plastic reduction in retail supply chains. Non-detectable carbon black trays are not suited to the existing recycling infrastructure in the UK and Ireland, and these were removed from our supply chain in 2019.
In 2020 we launched paper trays with a key customer across one of their products ranges. We continue to investigate paper as a potential alternative to plastic in trays to understand potential impacts and collate data to enable better decision making. Where paper-based options require the use of a laminate plastic film, in most cases the consumer must separate the plastic and paper components to allow the paper packaging to be recyclable. We are working to better understand the true route to disposal and the environmental impact of paper laminate as a viable alternative for rigid trays. Data and findings will be used to make informed, transparent decisions on the best long term sustainable solution.
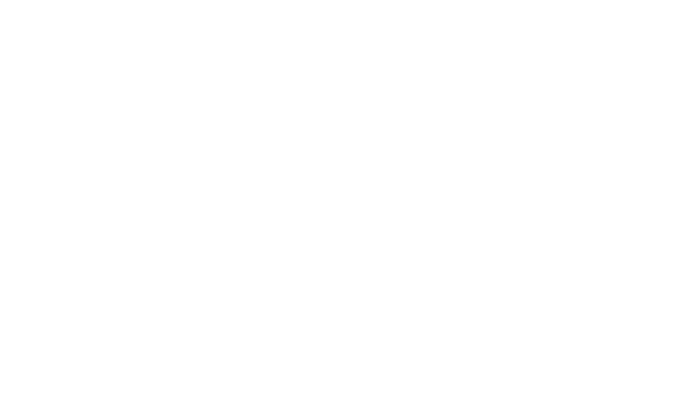
Polyvinylidene Chloride (PVdC) is a resin used in flexible plastic which provides an excellent barrier to oxygen and water vapour, delivering consistent product protection but is problematic for the recycling process. We are working on a project to understand the impact of removing PVdC content from plastic bags, and our findings will inform and enable the transition away from PVdC for retail use. We are also exploring the options on PVdC alternatives in business to business and industrial use, where waste streams are separate and more manageable.
Target Four:
All cardboard packaging to be Forest Stewardship Council (FSC) certified, or equivalent, by 2025
Paper packaging is primarily corrugated, solid board and carton board boxes which are used to transport our products.
100% of sourced corrugated packaging is now FSC certified.
Our target is to have the remaining cardboard packaging, typically solid board and carton board, FSC certified by 2025.
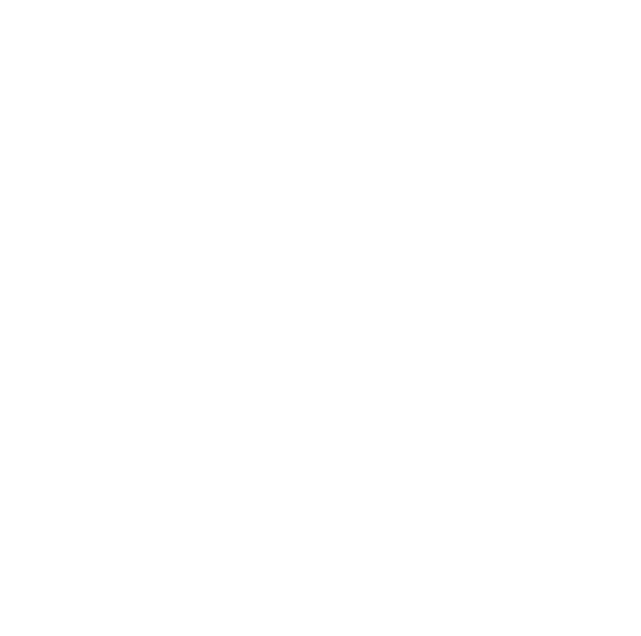